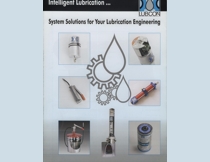 Lubrication of rolling bearings
Moment of friction in the bearings is determined by the type of camp, the load, speed and lubrication of the bearing. The biggest impact of friction in rolling bearings are lubrication. In practice, at least up through friction with grease lubrication. When oil lubrication plays a major role along with the viscosity and quantity of oil misleading to camp, but also the removal of oil outside the camp. The table shows how lubrication and lubricant according to the range of speed, expressed by parameter n.d (min - 1 mm) for different types of bearings.
Table: Ways and means for lubrication of rolling bearings |
|
|
Parameter for rotation speed |
Lubricator |
Way of lubrication |
(n.d) in min-1.mm |
Solid lubricant |
Lifetime |
1500 |
|
Extra |
|
|
Lifetime |
0,5.106; |
Grease |
Extra |
1.106 particularly suitable for greases |
|
Via Injection |
|
|
Oil bath |
0,5.106 |
Oil |
Recycling spreads through equity extraction mining of bearings or special items |
Must be determined individually |
(bigger quantity) |
|
Recirculating lubrication with pump |
1.106 |
|
By oil injection |
To 4.106 tested |
|
Pulse lubrication |
1,5.106 |
Oil |
Drip lubrication |
Depends on the bearing's type and viscous of oil quantity and the structural performance |
(minimum quantity) |
Oil mist |
|
|
Oil-air lubrication |
|
|
Air- oil lubrication |
|
Typically bearings are preserved dispersion (refrigerant oil - according to the company FAG). Conservation is tolerated by all means of spreading and should not be washed away during installation. Depending on the type of camp fuel anoint tool can be very different. In the axial bearing, with oil lubrication, there is a strong centrifugal effect and fuel oil is about 100 times greater than radial bearing to ensure minimal friction. The choice of lubricant is determined by speed and vision of the constructor for rational lubrication. Preferably lubricated with grease, if other considerations do not need oil lubrication or otherwise. If grease lubrication is essential for the normal operation of the camp is the amount of grease in the bearings.

Upon initial greasing of bearings for general use in n.d. < 50000min1.mm, bearing the free space is filled with grease. If the area around the camp is a great place retaining ring so close to the camp always have an extra amount of grease (from discarded it in its original rotation) or added grease inside the box around the camp. At high camps (nd> min-1.mm) fills only 20...30% of free bearing space to ensure easier sharing of grease in the bearing standing node. If you are doing spreads for the entire period of operation (for life) of the camp must ensure the presence of grease near the camp. When rotating the outer ring of the camp is only 15 % of the free bearing space is filled with grease. If the bearing operating temperature is higher, you must provide additional retention amount of grease around the bearing (fig. 5.23) with washers, forming enclosed spaces on both sides of the camp with a capacity of 3...5 times the volume of grease in the bearings.
The use of liquid lubricant for the lubrication of rolling bearings is recommended in applications which are characterized by high speeds and temperatures in the bearing unit, preventing the use of greases. In general, lubrication oil is relatively more difficult than with lubrication greases, but is also characterized by certain advantages such as better cooling of the bearing unit. Use mineral and synthetic oils. Choosing the right oil - Selection of appropriate oil case is based on determining the minimum required kinematic viscosity of the oil in order to properly lubricated. Crucial for optimum lubrication of a rolling bearing are given operating conditions. In cases where it is possible to assume that the bearing operating temperature is equal to 40 °C, determining the necessary kinematic viscosity of the oil is facilitated. for example, the rolling bearing has an average diameter dsr =380mm, speed n = 500min-1 and a working temperature of 70 °C. The minimum required kinematic viscosity of oil is determined on 11 mm2/s. For the bearing operating temperature equal to 40 °C, however, is appropriate to use oil with a kinematic viscosity of 32mm2/s. In all cases, to ensure optimum lubrication of the bearing, it is necessary to comply with the recommendations and methods for selecting the particular oil producer.
Replacement of the lubricant
The frequency of oil change depends primarily on the operating conditions selected scheme and quantity lubrication in the bearing unit. When oil bath lubrication sufficient oil change once a year, provided that the operating temperature does not exceed 50 °C and there is little risk of external contamination. When running the camp at a higher temperature requires more frequent oil changes, such as at 100 °C recommended replacement every 3 months. When circulating lubrication or lubrication spray interval recommended oil change be determined by regular diagnostic status of the oil. Lubrication Technologies, Liquid lubricant. There are many types of lubrication oils.
Among the most widely used is:
Oil bath lubrication. Oil bath lubrication, also known as crankcase lubrication (Fig.1) is considered the most elementary way for oil lubrication. Used for bearing units with horizontal shaft. The bearing housing assembly pouring a certain amount of oil, usually so that the oil level to reach the center of the bottom rolling element forming the bottom of the oil bath in which they submerged part of moving parts. With its rotation moving parts raise, spread butter and submit to the other moving parts of the bearing unit. This method of lubrication is recommended for values of the velocity factor A=200 000 n.dsr. mm.min-1, the speed of lubricating bearings should not exceed 10 000 min-1. A significant disadvantage of the oil bath lubrication is the inability to filter oil passing through the bearings, which makes it possible contamination and require its frequent replacement.
Lubrication spray. It is used in bearing assemblies with vertical and horizontal orientation of the shafts - Fig.2. As a principle, a spray lubrication is like oil bath lubrication, but the application requires the use of additional elements. On the rotating shaft is attached firmly or placed free disk or ring in its rotation sprayed oil on the bottom. In certain cases it can be done by spraying the oil on high speed gears.

Circulating lubrication. Provides a continuos supply of oil to the bearings - Fig.3. Typically, forced oil circulation is performed by an oil pump. Apply two methods. The first, used oil is fed back to camp. Also called closed circulation lubrication. In the second method the outside oil passes through the bearings after leaving camp unit where filtered and cooled. The method is known as the Flow Circulation lubrication. Circulating lubrication ensures better cooling of the bearing unit, as well as lubrication of all parts of the bearing unit.
Oil mist lubrication. This type of lubrication is very suitable for fast, light and medium loaded bearings, the speed of which can reach 35,000 to 40,000 min-1. Lubrication by oil mist supply provides the minimum necessary amount of oil (in some cases a decrease in oil consumption up to 5 times compared to other types of lubrication), camp of continuous cooling of air passing through it and oil pollution prevention as a result of created in the camp higher than atmospheric pressure. As a major drawback of the method can indicate the possibility of environmental contamination.
Injection lubrication. Lubrication via injection (Fig.4) is used in bearings, operating under very difficult conditions - speed, close to maximum, high loads and temperatures. These are usually heavily loaded bearings spindles of machine tools, bearings of water turbines, heavy duty motors. Essentially, lubrication spray is circulating lubrication flow reactor, which is accomplished through periodic submission of pressurized oil directly into the bearing in one more nozzles located next to it. Fundamental requirement for oil spray technology is to be submitted under a high enough speed to overcome the turbulence created by the rotating bearing. At low revolution and unloaded bearings are used more by hand, drip and the wick lubrication.
TURMOGREASE® Highspeed L 252
Fully synthetic; color - light beige ; operating temperature range - 40 ºС до + 120 ºС; compatible with nitrile rubber (NBR), FKM, PTFE and PA 6.6. Suitable for lubrication of spindle and cylindrical roller bearings with mesh sizes of inner d<100 mm. This grease is made especially for use in high speed bearings (min-1 x mm).
TURMOPLEX ® 2 TML Fully sunthetic; color - copper/clear; operating temperature range - 35 ºС до + 160 ºС; compatible with nitrile rubber (NBR), FKM, PTFE and PA 6.6. This effective grease for high temperatures, heavy loads and high speeds up to n x dm 1.3 mln. ( min-1 x mm) has been successfully used in spindles, electric motors, fans and also in small miniature bearings.
TURMOGREASE® Li 802 EP Partially synthetic; color - dark brown; operating temperature range - 35 ºС до + 140 ºС. Longer periods of change, quiet operation in unstable environments. Special grease for high loads, speads and loads for all types of roller and plain bearings, such as grinding stones machinery.
TURMOGREASE® Highspeed L 182 Fully synthetic; color - light beige; operating temperature range 70 ºС до + 120 ºС. Compatible with nitrile rubber (NBR), FKM, PTFE and PA 6.6. This lubricant is especially suitable for smaller roller bearings (d<25 mm) and very high speed by factor n x dm 2.2 mln (min-1 x mm) and also at very low temperatures and places with requirements for very high friction properties.
Auto and uploaded One-lubricator

Fully practical oriented program of accessories allows implementation in the lubricator LUBCON TURMOLUBE without any problems.
|